Many operators run Bitcoin mining hardware in harsh environments, where extreme temperatures, moisture, and dust can lead to miner failures. Effectively managing repairs is essential for running a profitable self-mining or hosting business. Whether considering 3rd party service providers, vertical integration, or a hybrid solution, this article aims to guide your decision-making process by delving into the following topics:
Three Main Strategies
3rd Party Service Provider
How to Identify a Quality 3rd Party Repair Service Provider
Time is of the Essence
Integrated Repair Department
Strategic Roadmap
Hybrid Solution
In Conclusion
In the Mining Insights Exchange series, Digital Mining Solutions invites guest writers to exchange ideas and expertise. This article Written by Jenn Hays, CEO of Orion & Taurus. Orion & Taurus specializes in delivering specialized education for ASIC miner repair.
Three Main Strategies
The approach to the repair process varies for each operator and relies on resources, location, and expertise. In this article, we will explore three strategies for implementing miner repair into your operations:
Utilizing a 3rd Party Service Provider: Working with an external company that specializes in ASIC miner repair services.
Vertical Integration: Establish a dedicated miner repair department within your company. Implement a streamlined approach that is independent of 3rd party service providers.
Hybrid Approach: Combine elements of both the first and second strategies to create a tailored approach that suits your specific needs.
3rd Party Service Provider
A common strategy is to utilize a 3rd party service provider for miner repairs. Operators may opt for this approach for various reasons:
Limited resources to dedicate specific personnel to miner repair.
A small workforce due to the size of the facility.
Technicians lacking expertise and time to devote to learning repair techniques.
Preference for lean operations and allocating capital to a 3rd party service provider.
How to Identify a Quality 3rd Party Repair Service Provider
Identifying a quality 3rd party repair service provider is crucial, as not all repair centers offer the same level of quality. Some may experience long lead times or return hardware with different hashboards. Here are three key elements to consider when evaluating a repair service:
Transparency: Full transparency is essential in a repair facility. Look for centers that implement processes to catalogue the serial numbers of each hashboard, PSU, and control board for every miner. A quality repair service provider may also maintain a detailed exhibit file, including pictures of the miners upon arrival and after cleaning. This allows clients to verify the condition of their miner and ensure that the same hashboards were returned to them.
Repair Statistics: Pay close attention to the repair statistics provided by the service provider. Be cautious of repair facilities boasting a 100% success rate, as this could indicate misleading claims. As outlined in a previous article by Orion & Taurus, not all boards can be fixed. Orion & Taurus, for example, achieves a success rate ranging from 75% to 90% depending on the type of miner.
Cleanliness: Another crucial aspect to consider, especially if you have the opportunity to visit the repair facility, is cleanliness. The environment should be clean, free of any food, and with closed tops on liquids in the workspace. Inquire about the service provider’s routine cleaning procedures for the job area, including each workbench. This ensures the prevention of FOD (Foreign Object Debris) from contaminating the boards and potentially causing latent damages.
Did you know that thorough cleaning of mining hardware before applying any heat to the hashboard can prevent latent damages from Foreign Object Debris (FOD)? Having a meticulous cleaning process is a crucial component of your repair service. You can learn more about the cleaning procedures at Digital Manuals. With Orion & Taurus’s cleaning procedures, every one out of three hashboards with an excessive amount of FOD were able to hash again.
Time is of the Essence
The longer the lead time for a repair, the higher the opportunity costs. To assist clients who prioritize a short turnaround time, Orion & Taurus introduced a “white glove service.” Under this service, clients could contractually send an agreed number of miners each month with a priority guarantee. Be sure to inquire whether the repair facility offers a similar service.
Integrated Repair Department
An integrated repair department can be situated on or near the mining site. This setup entails dedicated personnel responsible for locating and processing miners’ repairs, along with having diagnostic and micro-soldering procedures in place. Full integration necessitates the presence of all diagnostic equipment and micro-soldering workbenches.
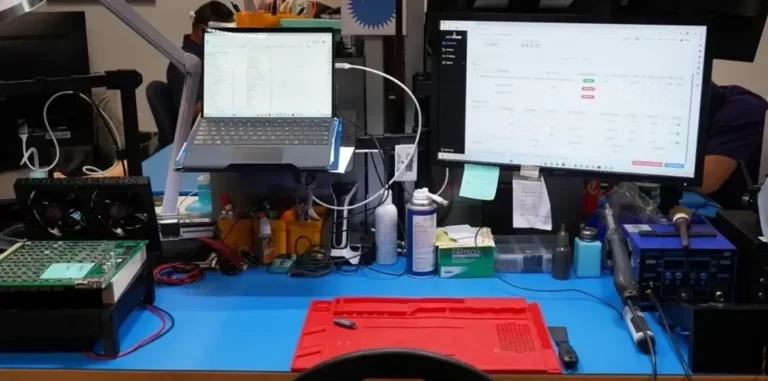
Orion & Taurus provided a price estimate for the equipment list used in their repair facility at $31,600 per workbench. This cost covers all diagnostic and cleaning supplies, as well as JBC micro-soldering tooling (excluding consumables). When contemplating the establishment of a fully integrated repair department, careful consideration of capital allocation is essential in the decision-making process. If the repair needs of your business exceed the combined expenses of equipment, education, and technician salaries, creating a vertically integrated repair department becomes a viable option. Alternatively, offering repair services to third parties can help justify the investment.
If you want to explore the equipment list in detail, visit the website of Orion & Taurus. Additionally, our educational materials, including manuals detailing our Standard Operating Procedures (SOPs) for cleaning, diagnostics, and micro-soldering processes, are available.
Strategic Roadmap
Integrating a repair department requires a strategic roadmap, which includes the following steps:
Identifying ASIC Miner Repair Techs: The first step involves identifying your ASIC miner repair technicians. Options include investing in your current operations’ personnel or hiring designated technicians to perform the repair process.
Teaching Diagnostic and Troubleshooting Procedures: The second step is to educate technicians on diagnostic and troubleshooting procedures in the miner repair process. According to Orion & Taurus, approximately 85% of the time is devoted to diagnostics.
Training in Micro-Soldering Techniques: Once the problem is identified during diagnostic procedures, machines proceed to the repair/rework stage. Training technicians in micro-soldering techniques cannot be mastered in a short period. Basic knowledge can accelerate the learning curve from 0% to 80%, but mastery requires continued practice over time.
Quality Assurance Process: After the repair/rework stage, miners undergo a Quality Assurance process to ensure that the work was done correctly.
Hybrid Solution
The hybrid solution is ideal if your operation falls somewhere in the middle. It involves personnel trained in cleaning and diagnostic procedures, enabling informed decisions on whether to proceed with repairs. If repair is chosen, hashboards can be taken to a Bitcoin miner repair facility. Alternatively, for simpler repairs like changing a temperature sensor, printed circuit board repair shops can be utilized. Onsite repair services are also available, providing the necessary data to determine if the miner is repairable.
Conclusion
There are various benefits to using 3rd party service providers. Mining operators can save time for other tasks, such as expansion. Additionally, a 3rd party repair center can provide detailed insurance reports based on miner history logs. However, using a 3rd party repair center means losing control over the final repair product and being subject to the repair facility’s timeline, potentially resulting in long wait times.
Vertical integration offers control over repair deliverables, enabling better management of time and work quality, as well as real-time updates on repair progress. This data facilitates informed decisions, especially when deciding whether to repair a miner due to its complexity. However, vertical integration requires significant capital investment, which may not be justified if there are insufficient repairs to justify acquiring all necessary equipment.
For some operators, the hybrid approach provides the best resource allocation balance. Whether considering 3rd party service providers, vertical integration, or a hybrid solution, Orion & Taurus is here to assist in your decision-making process.